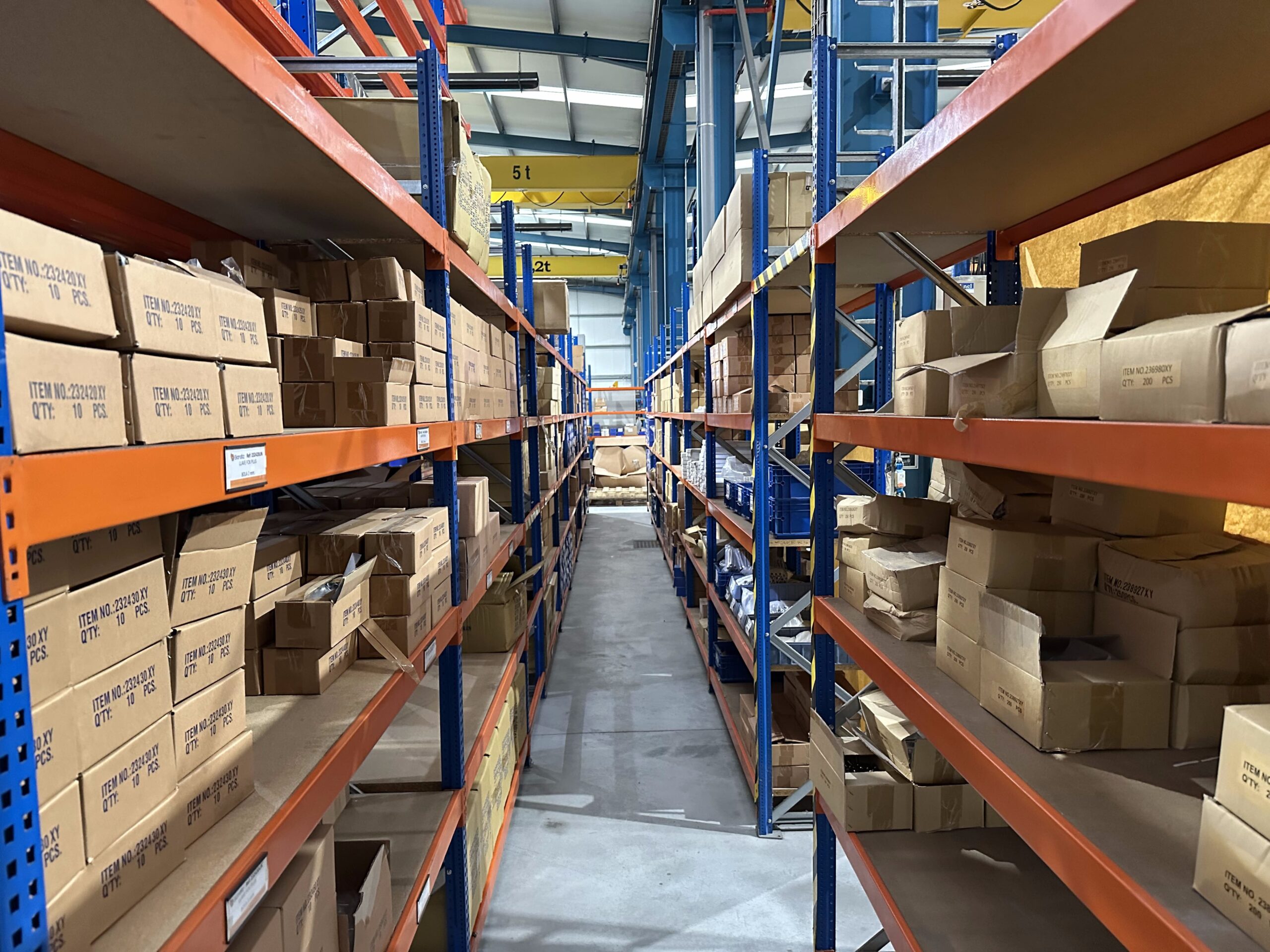
Continuous improvement initiatives in the warehouse to optimise the work processes.
At Bianditz, we are constantly looking for ways to improve our processes and offer the best possible service.
We are committed to operational excellence and customer satisfaction. As part of this commitment, we have implemented a series of continuous improvement initiatives in our warehouse, focused on optimising our dispatches, delivery times and the layout of our facilities.
¿What have we changed?
Previously, many of our most sought-after products were on a two-storey shelf, which required climbing stairs every time someone needed to access the second level. This system was not only time consuming, but also made access less efficient.
Now, we have reorganised everything on shelves at floor level, prioritising accessibility and speed. This allows us to:
- Layout improvement: A strategic restructuring of our warehouse layout has allowed us to maximise the use of space and improve workflow.
- Dispatch optimisation: Improving the layout has helped us refine our dispatch processes to ensure that each order is handled with the utmost accuracy and speed. This allows us to reduce errors and ensure that products reach our customers in perfect condition and on time.
- Reduced lead times: Both expediting optimisation and improved layout have been key to reducing order processing and delivery times. Our customers can now enjoy a faster and more efficient service.
At Bianditz, we believe there is always room for improvement. We continue to work every day to improve our processes and ensure that our logistics are up to your needs.