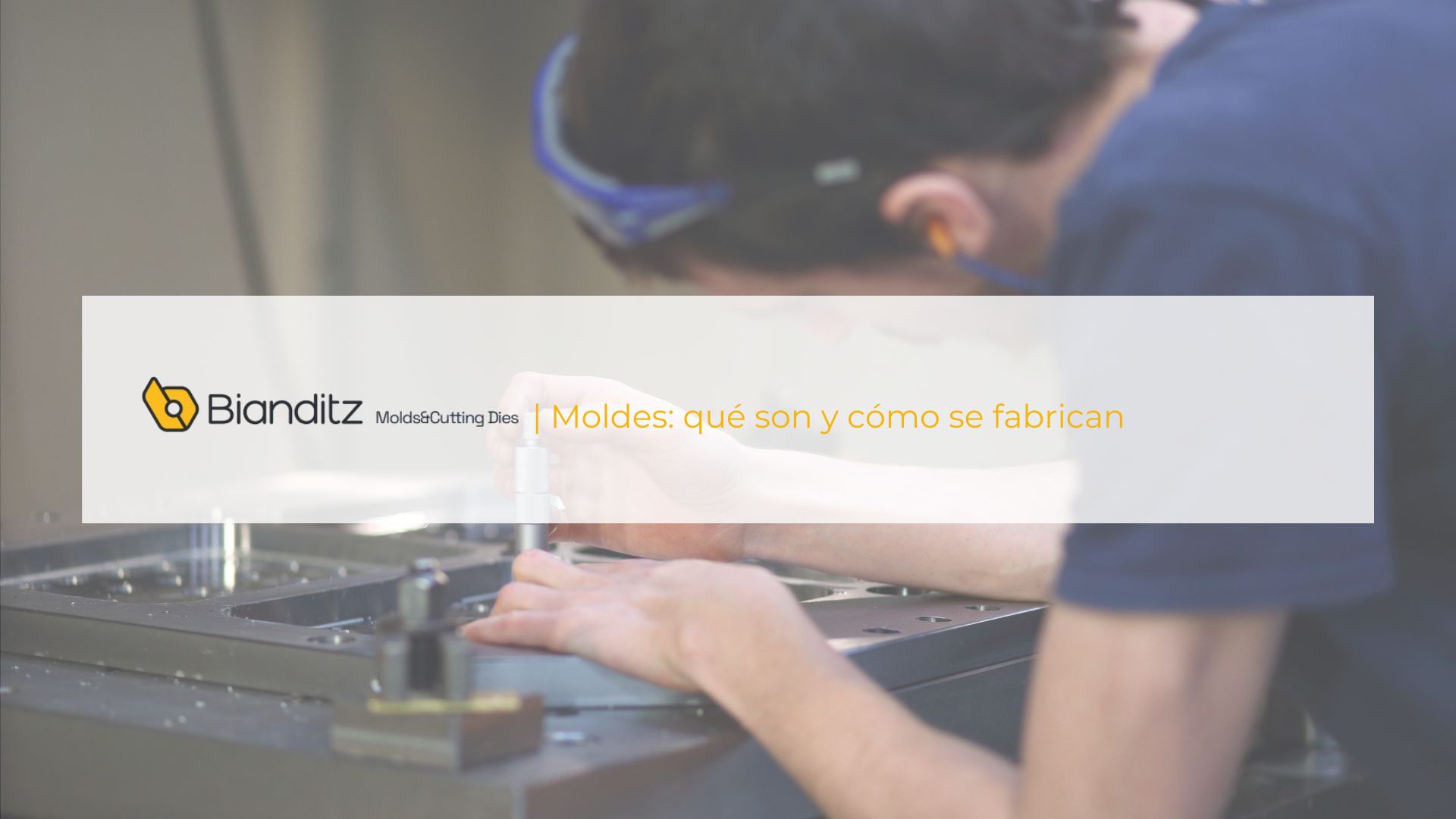
Industrial Molds: What Are Industrial Molds and How Are They Made at Bianditz?
Industrial Molds: What Are Molds and How Are They Made at Bianditz?
At Bianditz Molds & Cutting Dies, we specialize in the manufacturing of high-quality industrial molds using injection and compression, including rubber injection molds and rubber-metal molds. In this article, we will explain what molds are, their role in manufacturing processes, and how we produce them in our facilities.
What are industrial molds and what are they for?
Molds are essential tools in industrial manufacturing that are used to shape materials through the use of pressure, heat, and time. This process is essential in various industries, such as the automotive, electrical, white goods, and agricultural sectors. Molds allow the creation of products with precise and consistent shapes, and their use is essential when working with materials such as rubber, plastics, metals, and other composites.
What Materials Are Industrial Molds Made From?
At Bianditz, we manufacture steel molds for rubber parts mainly, however, depending on the client’s needs, molds are made for later use with materials such as metal and, in limited cases, plastic.
The parts made from our steel molds can be made from the following materials:
- Rubber: Ideal for applications where high elasticity and wear resistance are required.
- Rubber-metal: In these cases, the rubber part has a metal insert, usually made of aluminum or magnesium, to improve the durability and strength of the final part.
- Plastic: To a lesser extent, some parts may incorporate plastic inserts to improve specific product properties.
The Mold Manufacturing Process in Bianditz
Bianditz mold manufacturing follows a detailed process to ensure precision and quality in each piece. Below we describe the main phases of the process:
- Mold design: The process begins with the design of the mold to be manufactured, which will be adjusted to the client’s specifications and the needs of the final product.
- 3D Design: With the design of the part, a 3D model of the mold is created, which allows to verify the shape, size and cavities necessary for the manufacture of the part.
- Material selection: In this phase, the appropriate materials are selected according to the characteristics required for the final piece.
- CAM programming: The CNC machine is prepared for manufacturing using CAM programming. In this phase, the operator checks and centres the material in order to proceed to prepare the mold.
- Mold manufacturing: The mold is manufactured and may include several cavities depending on the desired production volume. Manufacturing can be done by injection or compression, as we will see below.
- Adjustment and assembly: Finally, the verification is carried out, and after ensuring that everything is correct, the mold is assembled.
Types of Molds: Compression vs. Injection
These molds can be used to manufacture parts using two main techniques: compression molding and injection molding. Each of these methods has advantages depending on the type of part to be manufactured. Below we explain both processes in detail (this process is NOT carried out at Bianditz).
Compression MoldingCompression molding is a technique used for larger parts or when specific heat resistance properties are required. This process is mainly used when parts have complex shapes or when the material must be subjected to pressure during processing. It is more manual and usually more expensive due to the preheating and pressing steps. In this case the material, generally in the form of blocks or granules, is heated to a suitable temperature so that it becomes malleable and fluid. After this, the mold is loaded, the tempered material is placed into the open mold that is shaped like the final part. The mold is closed and pressure is applied to force the material to completely fill the cavity. Depending on the material, additional heat may be applied to cure the part. After the material has taken the desired shape, it is cooled and the part is removed from the mold. |
Injection MoldingInjection molding is a faster process than compression molding, especially when it comes to manufacturing parts in multi-cavity molds for high volumes. In this process, the material (usually rubber) is injected into the closed mold, filling all the cavities of the mold. In this case the molding process is different, the material, usually in the form of granules, is melted or melted at the appropriate temperature. The material is then injected, using a nozzle, into the cavities of the closed mold. Once the material has filled the cavities, the mold is cooled, allowing the material to solidify and take the final shape. Finally, once cooled, the mold is opened and the molded parts are removed. You can read more in the post “Rubber injection molds: innovation and precision for the industry”. |
At Bianditz, we specialize in offering high-quality, customized solutions for every type of mold and application. If you are looking for precise and efficient industrial molds for your production, contact us and find out how we can help you.