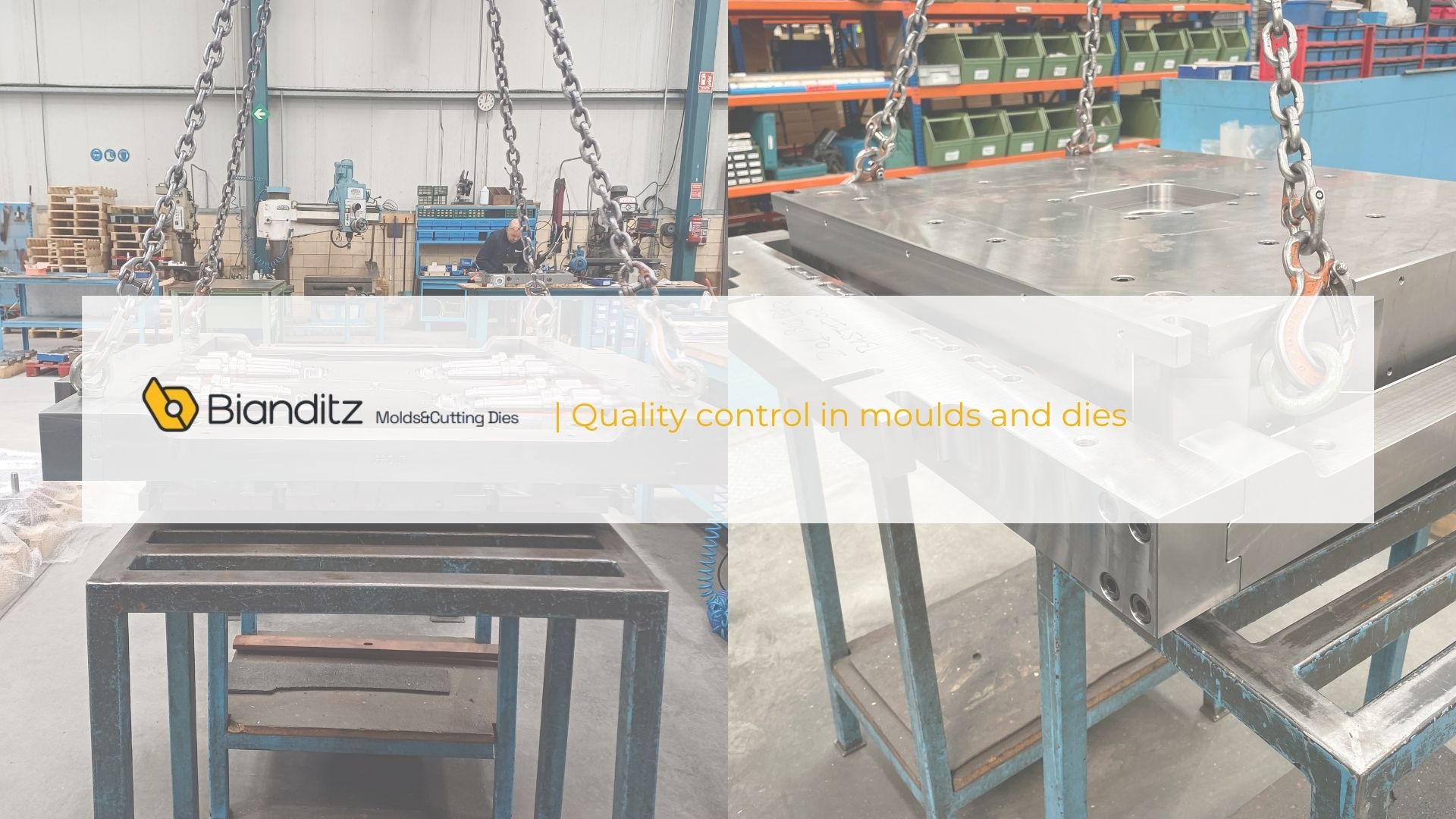
Quality control in molds and cutting dies: precision before delivery
Quality control in molds and cutting dies: precision before delivery
At Bianditz, as injection mold makers and manufacturers of cutting and bending dies, we know that quality is not an option, but a requirement. Whether it is injection molds for rubber, metal or aluminium, or dies for punching, cutting or bending, every project must meet the highest standards before it leaves our premises.
Industrial molds for rubber and metal: control before delivery
Before any mold is delivered, we carry out a thorough check that allows us to guarantee its performance under real conditions. For some molds, we use a thermal verification system with BCR, where the mold is inserted into a specific part and oil is injected at 90°C for 2-3 days. This allows us to detect possible leaks, escapes or internal imperfections that could compromise production.
This procedure is particularly important in the manufacture of customised industrial rubber molds, where any deviation can affect the sealing, filling or durability of the final part.
Contact accuracy in dies and molds
In addition to the thermal test, we carry out a visual and mechanical check: we paint the base of the mold and join it to the upper part. If there are unpainted areas when separating them, we immediately detect the non-contact areas and adjust them to ensure the correct flow of material.
In the case of dies for profiling lines and dies for industrial lines, another method is used where precision in closing is key to obtaining clean cuts and accurate folds.
At Bianditz, control means attention to detail. That’s why our precision injection molds and dies come ready to integrate into demanding environments, with no margin for error.